Hlavní články Posuzování rizika při projektování elektrických zařízení strojů Rozhodujícím podnětem k napsání tohoto příspěvku byla poměrně rozsáhlá diskuse o problematice posuzování rizika u strojních zařízení pro stanovení vhodných kategorií požadavků na bezpečnostní části elektrických řídicích systémů, která v užším kruhu zainteresovaných elektrotechniků vznikla bezprostředně po skončení elektrotechnického semináře Rizika a bezpečnost strojních zařízení (prosinec 2001, Hradec Králové). Zmíněná diskuse potvrdila skutečnost, že ze strany státních orgánů nestačí jen vydávat nové zákony, technické předpisy a normy a nějak kontrolovat jejich dodržování, ale že je také nutné systematicky podporovat zavádění nových předpisů do praxe, a to hlavně kvalifikovaným výkladem jejich ustanovení a poskytováním metodiky jak pro splnění jejich požadavků, tak pro kontrolu dodržování stanovených „pravidel hry“. Vzhledem k tomu, že státní orgány zatím nic takového nečiní a zdá se, že ani činit nehodlají, je tento článek pokusem alespoň trochu přispět ke zlepšení informovanosti elektrotechniků v dané oblasti. Článek je určen především projektantům elektrických zařízení strojů, protože hlavně jich se dotýká problematika stanovení vhodných kategorií požadavků na bezpečnostní části elektrických řídicích systémů v závislosti na posouzení (nebo alespoň odhadu) rizika, které je spojeno s provozem strojního zařízení. Dále uváděný příklad je pro větší srozumitelnost hodně zjednodušen a popisuje jen jeden z možných způsobů řešení problému, to znamená, že pro stanovení kategorií požadavků a vyhodnocení účinnosti ochranných opatření mohou být použity i jiné postupy a metody. V žádném případě není smyslem článku poskytnout univerzální, podrobný a vyčerpávající návod na řešení dané problematiky. Jde spíše o to, názorně ukázat, že odpovědný návrh elektrických řídicích obvodů pro bezpečnostní funkce strojních zařízení a výrobních systémů není v současné době úplně jednoduchou záležitostí, a přimět projektanty (ale nejen je) k veřejné diskusi na toto téma. Nové chápání bezpečnosti strojů Termíny stroje a strojní zařízení zahrnují v současné době značně rozsáhlý sortiment technických zařízení, jejichž charakteristickou vlastností je dominance mechanických nebezpečí, která jsou vyvolávána pohybujícími se částmi (nejméně jednou). Mezi strojní zařízení patří také sestavy strojů (technologická zařízení), které je možné výstižněji označit jako výrobní systémy, což je také jeden z termínů, které jsou použity v normě ČSN EN 60204-1 Bezpečnost strojních zařízení. Elektrická zařízení pracovních strojů. Část 1: Všeobecné požadavky. Uvedená norma (typu B1) patří do rozsáhlé skupiny bezpečnostních norem pro strojní zařízení, které jsou přejímány do českého právního systému z evropské legislativy a vyžadují uplatňování zcela nových přístupů k řešení problematiky bezpečnosti strojních zařízení. Z pohledu těchto, pro mnoho elektrotechniků nových norem jsou složitější technická zařízení chápána jako objekty (systémy) složené z funkčně vzájemně vázaných částí, přičemž výsledná úroveň bezpečnosti systému (celku) více či méně závisí na úrovni bezpečnosti dílčích částí zařízení. Vzhledem k tomu, že u moderních a vysoce automatizovaných strojů je bezpečnost strojního zařízení jako celku obvykle zajišťována hlavně pomocí bezpečnostních funkcí, které jsou vykonávány elektrickými řídicími systémy, je zřejmé, že elektrické zařízení významným, ne-li rozhodujícím způsobem ovlivňuje bezpečnost celého stroje (systému). Je proto zcela logické, že čím více závisí bezpečnost strojního zařízení jako celku na elektrických řídicích obvodech pro bezpečnostní funkce a čím větší jsou rizika vyplývající z nebezpečí, proti nimž elektrické bezpečnostní obvody zajišťují ochranu, tím vyšší požadavky jsou ze strany bezpečnostních norem kladeny na schopnost takových obvodů a jejich součástí odolávat závadám, které by mohly být příčinou nefunkčnosti obvodu (ztráty bezpečnostní funkce). Touto tzv. funkční bezpečností se zabývá zvláštní norma ČSN EN 954-1 (ale i jiné). Kategorie požadavků na bezpečnostní části řídicích systémů ČSN EN 954-1 Bezpečnost strojních zařízení. Bezpečnostní části řídicích systémů. Část 1: Všeobecné zásady pro konstrukci (rovněž typu B1) obsahuje základní bezpečnostní požadavky, pokyny a zásady pro konstrukci bezpečnostních částí řídicích systémů strojů. Pro tyto části norma definuje pět kategorií požadavků (B, 1, 2, 3, 4) s ohledem na odolnost vůči závadám a popisuje charakteristiky jejich bezpečnostních funkcí, tj. chování při výskytu závady. Tuto normu je možné použít pro všechny bezpečnostní části řídicích systémů, bez ohledu na druh použité energie, např. elektrické, hydraulické, pneumatické, mechanické. Norma ČSN EN 954-1 nespecifikuje, které bezpečnostní funkce a které kategorie musí být použity v jednotlivých konkrétních případech, a vezme-li se v úvahu obrovská rozmanitost strojních zařízení a s nimi spojená, často velmi specifická nebezpečí, ani to není možné. Přesné specifikace kategorií požadavků pro bezpečnostní obvody lze najít pouze v normách typu C, zpracovaných přímo pro jednotlivé stroje nebo skupiny strojů. V případě, že je navrhováno elektrické zařízení stroje, pro který neexistuje norma typu C, musí vhodnou kategorii požadavků pro konkrétní bezpečnostní funkci na tomto stroji vždy zvolit konstruktér, tedy např. projektant elektrického obvodu blokovacího zařízení ochranného krytu. Má-li být jeho volba kvalifikovaná, musí vzít v úvahu nejen všechna dílčí nebezpečí, proti kterým zajišťuje projektovaný obvod ochranu, ale také úroveň všech nebezpečí, která jsou uvažována. Při úvahách o nebezpečích, která jsou spjata s konkrétním strojem, je nezbytně nutné důsledně rozlišovat různé existenční fáze zařízení, neboť obvykle významným způsobem ovlivňují možnost výskytu nebo úroveň dílčích nebezpečí, popř. svým charakterem vytvářejí rozdílné předpoklady pro vznik nebezpečných situací a událostí. Uvažování různých nebezpečí Přehledný a značně obsáhlý soupis nebezpečí, nebezpečných situací a nebezpečných událostí, které je nutné obecně uvažovat v souvislosti se strojními zařízeními, je uveden v tabulce A1 informativní přílohy A normy ČSN EN 1050 Bezpečnost strojních zařízení. Zásady pro posouzení rizika. Na tomto místě je zapotřebí upozornit na skutečnost, že nejnovější verze této normy typu A (ze srpna 2001) zavádí – v porovnání s původní normou – jinou terminologii a odlišné definice: termín poškození byl nahrazen termínem škoda a je definován jako fyzické zranění nebo poškození zdraví nebo majetku; termín riziková událost byl nahrazen termínem nebezpečná událost a je definován jako událost, která může být příčinou škody; termín riziko byl nahrazen termínem nebezpečí a označuje zdroj možné škody (obvykle je používán ve spojení s dalšími slovy, která definují původ nebo charakter očekávané škody); termín rizikovostbyl nahrazen termínem riziko a je chápán jako kombinace závažnosti možné škody v určité nebezpečné situaci a pravděpodobnosti vzniku této situace. V tabulce A1 informativní přílohy A normy ČSN EN 1050 jsou nebezpečí rozdělena podle druhu do různých skupin, např.: - nebezpečí mechanická,
- nebezpečí elektrická,
- nebezpečí tepelná,
- nebezpečí vytvářená hlukem,
- nebezpečí vytvářená vibracemi,
- nebezpečí vytvářená zářením,
- nebezpečí vytvářená materiály a látkami,
- nebezpečí vznikající zanedbáním ergonomických zásad pro konstrukci stroje,
- nebezpečí vznikající při poruchách a při přerušení dodávky energie,
- kombinace různých nebezpečí,
- nebezpečí vyvolaná mobilitou,
- nebezpečí vznikající při zdvihání,
- nebezpečí vznikající při zdvihání a přepravě osob,
- nebezpečí vznikající při práci v podzemí,
- jiná další nebezpečí (výčet není úplný).
Každá skupina nebezpečí je označena základní číslicí, další číslicí (za tečkou) jsou podrobněji charakterizovány jednotlivé nebezpečné události (např. 1 je označení pro skupinu mechanických nebezpečí, ve které 1.1 označuje nebezpečí stlačení nebo rozdrcení, 1.2 označuje nebezpečí střihu atd.). Většina projektantů elektrických zařízení strojů se při své činnosti nesprávně soustřeďuje pouze na nebezpečí, která přímo vyplývají z použití elektrické energie nebo jejího vzniku (tato skupina nebezpečí je v ČSN EN 1050 označena číslicí 2) a mohou být vyvolána: 2.1 dotykem osob s živými částmi elektrického zařízení (zkráceně tzv. přímým dotykem), 2.2 dotykem osob s částmi elektrického zařízení, které se staly živými v důsledku závady (zkráceně tzv. nepřímým dotykem), 2.3 přiblížením osob k živým částem s vysokým napětím, 2.4 elektrostatickými jevy, 2.5 tepelným zářením nebo jinými jevy, jako je např. odlet roztavených částic a chemické účinky zkratů, přetížení apod. Požadavky a ustanovení pro ochranu před uvedenými elektrickými nebezpečími jsou velmi podrobně popsány v normě ČSN EN 60204-1, zejména v článcích 6, 7 a 8, a jejich splnění je pro zkušené projektanty elektrických zařízení zcela rutinní záležitostí. Ve všeobecných požadavcích, které jsou popsány v článku 4 normy ČSN EN 60204-1 je ovšem uvedeno, že rizika spojená s nebezpečími vyplývajícími z elektrického zařízení musí být posuzována (jen) jako část všech požadavků z hlediska posuzování rizika celého stroje, přičemž toto ustanovení je vlastně odkazem na normu ČSN EN 1050. Podle výsledku posouzení se určí přijatelná úroveň rizika (tzv. mezní riziko) a zvolí se vhodná ochranná opatření pro ochranu osob, které mohou být vystaveny těmto nebezpečím, samozřejmě to všechno při zajištění potřebného výkonu stroje. Mezi uvažovaná nebezpečí (výčet zdaleka není úplný) lze podle normy zahrnout: poškození nebo závady na elektrickém zařízení stroje, které mohou být příčinou úrazu elektrickým proudem nebo požáru, poškození nebo závady v řídicích obvodech (popř. na jejich součástech a souvisejících přístrojích), které mohou mít za následek chybnou funkci stroje, poruchy nebo přerušení vnějšího přívodu energie a poškození a závady v silových obvodech, které mohou mít za následek chybnou funkci stroje, ztráta spojitosti obvodů závislých na kluzných nebo valivých kontaktech, která může mít za následek poruchu bezpečnostní funkce, elektrická rušení (např. elektromagnetická, elektrostatická, rádiová) vyvolaná vně nebo uvnitř stroje, která mohou mít za následek chybnou funkci buď vlastního stroje nebo jiných strojů, nahromadění energie (jak elektrické, tak mechanické), které může být příčinou neočekávané funkce stroje. Je zřejmé, že pouze první z uvedených bodů se vztahuje k elektrické a požární bezpečnosti, zatímco ostatní body se týkají funkční bezpečnosti zařízení. Podrobněji se problematikou řídicích funkcí při poruše zabývá článek 9.4 normy ČSN EN 60204-1, přičemž ve Všeobecných požadavcích, uvedených v článku 9.4.1, lze najít ustanovení, že tam, kde může poškození nebo porucha elektrického zařízení způsobit nebezpečný stav nebo může být příčinou poškození stroje či zpracovávaného výrobku, musí být učiněna přiměřená opatření k omezení pravděpodobnosti vzniku takových nebezpečí. Druh opatření a rozsah, ve kterém jsou tato opatření buď jednotlivě nebo v kombinaci uplatněna, závisejí na úrovni rizika, které je spojeno s konkrétní aplikací, přičemž obecné pokyny pro volbu ochranných opatření je možné najít v základních bezpečnostních normách typu A (ČSN EN 292-1 a ČSN EN 292-2). Prostředky k omezení rizika při poruše elektrického zařízení stroje jsou popsány v článcích 9.4.2 a 9.4.3 ČSN EN 60204-1. Volba a konstrukce ochranného zařízení K ochraně osob před zbytkovým rizikem, které nelze odstranit projektovým omezením rizika, se používají bezpečnostní ochranná opatření spočívající v použití specifických technických prostředků, které jsou označovány jako bezpečnostní ochranná zařízení nebo také jako bezpečnostní ochrana. Ve většině aplikací je účinnost těchto ochranných zařízení do značné míry závislá na elektrické části řídicího systému stroje, a je proto nutné, aby projektanti elektrických zařízení strojů znali všechny předpisy, které jsou pro tuto oblast významné. Základními předpoklady pro kvalifikovanou volbu a konstrukci bezpečnostního ochranného zařízení pro konkrétní stroj jsou však nejen znalosti požadavků příslušných bezpečnostních předpisů, ale také zkušenosti konstruktérů se zajišťováním bezpečnosti obdobného typu strojního zařízení a detailní představa o průběhu pracovního procesu. Velmi důležitá je také kvalitní souhra mezi konstruktérem mechanické části ochranného zařízení (např. krytu) a konstruktérem souvisejících elektrických obvodů (např. blokovacího zařízení), popř. ještě mezi tvůrcem programového vybavení (je-li jádrem řídicího systému programovatelné elektronické zařízení). Při návrhu oddělujících ochranných zařízení, která vytvářejí fyzickou (hmatatelnou) bariéru zabraňující zásahu nebo přístupu osob do nebezpečného prostoru (např. ochranné kryty apod.), je nutné respektovat speciální normy, např. ČSN EN 953, ČSN EN 1088, ČSN EN 294, ČSN EN 999. Poslední dvě uvedené normy jsou zvláště důležité pro výpočet minimální bezpečné vzdálenosti při navrhování neoddělujících ochranných zařízení, která na hranicích nebezpečného prostoru nevytvářejí fyzickou překážku, ale vypnutím zastavují stroj nebo jeho části (nebo jinak zajišťují uvedení stroje do bezpečného stavu), jestliže se osoba nebo část jejího těla ocitne za bezpečnostní hranicí (např. AOPD, AOAPD, taktilní rohože (dotykové), dvouruční ovládací zařízení apod.). Pro správnou konstrukci a použití těchto ochranných zařízení je nutné, aby konstruktéři znali další normy, např. ČSN EN 61496-1 a ČSN EN 574. O tom, zda bude použito oddělující nebo neoddělující ochranné zařízení, musí konstruktéři stroje rozhodnout podle charakteru všech nebezpečí, proti kterým ochranné zařízení zajišťuje ochranu, a na základě znalosti způsobu obsluhy, popř. konkrétního umístění stroje. Alibisticky by bylo možné prohlásit, že toto není starost projektanta elektrické části stroje, avšak vzhledem k tomu, že se jedná o týmovou práci, nelze problém takto zjednodušovat a navíc, k odpovědnému rozhodnutí stačí docela prostě používat „selský rozum“ (alespoň podle mého názoru). U většiny strojních zařízení se vyskytují existenční fáze vyžadující vyřazení ochranných zařízení a umožnění spouštění nebezpečných pohybů stroje, přestože bezpečnostní ochrana neplní svoji funkci, např. při seřizování stroje, učení robotů apod. V takových případech je nutné použít další bezpečnostní ochranná opatření, která minimalizují riziko vyplývající z vyřazení ochranných zařízení, např. tlačítko souhlasného ovládání, redukci rychlosti, nutnost nepřetržitého působení na ovládače atd. Řešení problematiky vyřazení ochranných zařízení a minimalizace z toho vyplývajícího rizika jsou téměř výhradně záležitostí projektanta elektrického zařízení stroje. Už při návrhu a konstruování bezpečnostního ochranného zařízení musí konstruktéři řešit i problém, jakým způsobem bude účinnost tohoto zařízení ověřována a kdo ji bude ověřovat. Z hlediska elektrické části stroje to znamená, že např. pro měření doběhu mechanických částí musí být v elektrickém zařízení k dispozici vhodné připojovací body, popř. vhodné kontakty potřebné pro připojení měřicí techniky, a dokumentace musí obsahovat všechny potřebné informace. Ověřování Konstrukce bezpečnostních částí řídicího systému (např. elektrických obvodů pro bezpečnostní funkce) musí být ověřena. Smyslem ověřování je určení úrovně shody bezpečnostní části řídicího systému s bezpečnostními požadavky, které jsou pro dané strojní zařízení stanoveny příslušnými předpisy. Při ověřování se především musí prokázat, že každá bezpečnostní součást splňuje: - všechny požadavky příslušné kategorie,
- určené bezpečnostní charakteristiky stanovené zásadami pro konstrukci.
Bezpečnostní součásti jsou ověřovány jak analyticky, tak zkouškami stanovených bezpečnostních funkcí a stanovených kategorií, a proto je nutné vytvořit tzv. plán validace, ve kterém je stanoveno, jakými analýzami a jakými zkouškami bude potvrzena shoda technického řešení (jeho bezpečnostních vlastností) s danými požadavky. V každém případě musí být ověřeno, že: - všechny výstupní signály vyvolávané vstupními signály a mající vztah k bezpečnosti jsou správné a logické,
- chování při vzniku závady odpovídá stanovené kategorii požadavků,
- řídicí systém a všechny ostatní části zařízení jsou dostatečně dimenzovány s ohledem na předpokládané vnější vlivy.
Jsou-li při konstrukci bezpečnostních částí řídicího systému použita programovatelná elektronická zařízení, je při zkouškách nutné simulovat závady, u kterých při analýze vznikly pochybnosti. Tento požadavek vyplývá ze skutečnosti, že v současné době se zdá být obtížné, ne-li nemožné, s určitostí stanovit, zda může být zajištěna spolehlivá funkce jedinou větví programovatelného elektronického zařízení v případech, kdy může vadou (selháním) řídicího systému vznikat značné nebezpečí. Dokud nebude tento problém vyřešen, není vhodné spoléhat výhradně na správnou funkci programovatelného elektronického zařízení s jedinou větví (PLC standard). Po vykonání a ukončení všech analýz a zkoušek musí být vystaven tzv. validační protokol, který musí obsahovat potřebné informace o všech: - předmětech analýz a zkoušek,
- osobách, které analýzy a zkoušky prováděly,
- zkušebních zařízeních, včetně údajů o kalibraci a zařízeních pro simulaci závad,
- vykonaných analýzách a zkouškách,
- definovaných problémech a způsobech jejich řešení,
- výsledcích analýz a zkoušek.
Je také potřebné ověřit účinnost použitých bezpečnostních opatření, např. absolutním bodovým hodnocením úrovně rizika před opatřením a po opatření. V dále uváděném příkladu je popsána velmi jednoduchá grafická metoda umožňující hodnotit úroveň rizika v rozsahu 0 až 10 bodů, která byla s úspěchem ověřena na mnoha strojních zařízeních různých typů. Již zmíněné dokumenty jsou vyžadovány v příloze č. 3 nařízení vlády č. 170/1997 Sb., ve znění pozdějších předpisů, přičemž zvláště důležitý je popis metod přijatých pro odstranění nebo omezení nebezpečí způsobovaných strojním zařízením. Odhad rizika Z předchozích odstavců zcela jednoznačně vyplývá, že posouzení rizika souvisejícího s projektovaným strojem nebo strojním zařízením je neodmyslitelným prvním krokem kvalifikovaného návrhu konstrukčního řešení elektrických řídicích obvodů pro bezpečnostní funkce. Pro stanovení kategorií požadavků na bezpečnostní části řídicího systému (elektrické bezpečnostní obvody a jejich součásti) stačí udělat jednoduchý odhad rizika pomocí grafické metody, která je popsána v informativní příloze B normy ČSN EN 954-1. Pro odhad rizika touto zjednodušenou metodou se používají tyto tři pomocné parametry: S – závažnost možného zranění, F – četnost přístupu do nebezpečného prostoru a/nebo doba ohrožení, P – možnost vyvarování se rizika. Příloha B ČSN EN 954-1 rovněž obsahuje návod pro volbu stupňování pomocných parametrů. Zjednodušený postup pro volbu kategorií požadavků uvedený v této příloze však musí být chápán jen jako součást posouzení celkového rizika strojního zařízení podle zásad, které jsou uvedeny v ČSN EN 1050, nikoliv jako jeho náhrada. Odhad rizika zásadně vychází z předpokladu, že nejsou použita žádná ochranná opatření, neboť hlavním smyslem odhadu je stanovit nároky na konstrukci elektrických obvodů, které zajišťují funkci bezpečnostních ochranných zařízení z hlediska jejich odolnosti vůči závadám. Čím vyšší je odhadnuté riziko, tím náročnější jsou požadavky příslušné kategorie a tím vyšší také musí být odolnost příslušného elektrického bezpečnostního obvodu vůči závadám (tím menší musí být pravděpodobnost, že bezpečnostní obvod v důsledku závady selže). Odhad rizika musí být vždy vypracován: - pro každé jednotlivé nebezpečí,
- v každém jednotlivém nebezpečném prostoru,
- pro každou uvažovanou existenční fázi strojního zařízení.
Je tedy nezbytně nutné definovat všechny nebezpečné prostory, v nich identifikovat jednotlivá nebezpečí a rozhodnout, které existenční fáze stroje budou uvažovány. Příklad Dále je jako příklad popsáno použití odhadu rizika a následné stanovení kategorie požadavků podle ČSN EN 954-1 při návrhu některých elektrických řídicích obvodů obráběcího stroje s řízením CNC, který je určen pro rotační obrábění kovů za studena a umožňuje činnost v obráběcím nebo seřizovacím režimu, přičemž vkládání, upínání a vyjímání obrobků jsou ruční. Většina elektrotechniků si takový stroj určitě umí představit a navíc je snadné porovnat závěry v příkladu, učiněné na základě použití postupů podle obecných norem typu A, B, s požadavky norem typu C, které jsou již pro stroje CNC k dispozici. V automatickém pracovním cyklu (při obráběcím režimu) je ručně vložen a upnut obrobek, potom je spuštěn automatický naprogramovaný navazující cyklus obrábění a po jeho skončení je obrobek opět ručně vyjmut. Při navoleném seřizovacím režimu může obsluha provádět seřízení (např. programování, zkoušení a ručně řízenou nenavazující činnost) pro následný proces obrábění. Běžná obsluha popsaného obráběcího stroje je velmi jednotvárnou a monotónní činností, a jestliže by nebyla přijata žádná bezpečnostní ochranná opatření ke snížení rizika, bylo by velmi pravděpodobné, že dříve či později dojde k úrazu, např. vlivem nepozornosti, únavy apod. (statisticky je prokázáno, že na asi tisíc správných úkonů připadá jeden úkon chybný). Zdrojem největšího rizika jsou pohyblivé části stroje, které se přímo zúčastňují pracovního procesu, a na ochranu obsluhy před převážně mechanickými nebezpečími, jejichž příčinou jsou nebezpečné pohyby, musí být použita vhodná bezpečnostní ochranná opatření, přednostně technického charakteru, tj. bezpečnostní ochranná zařízení. Proto je nutné na stroji přesně vymezit všechny prostory v blízkosti pohyblivých částí, tzv. nebezpečné prostory, a v nich identifikovat všechna jednotlivá nebezpečí. Pro dosažení větší srozumitelnosti je dále jako jediný nebezpečný prostor uvažován hlavní pracovní prostor stroje, ve kterém se nacházejí např.: - otáčející se obrobkové vřeteno s upínacím zařízením,
- nástroje pohybující se v několika osách,
- revolverová nástrojová hlava atd.
V tomto nebezpečném prostoru je možné identifikovat množství jednotlivých nebezpečí, jejichž příčinou jsou pohyblivé části stroje, např.: - nebezpečí stlačení (rozdrcení) mezi pevnou a pohyblivou částí stroje,
- nebezpečí střihu (ustřižení) mezi pevnou a pohyblivou částí stroje,
- nebezpečí říznutí (uříznutí) v průběhu pohybu nástroje,
- nebezpečí zachycení a následného navinutí nebo vtažení pohybujícími se částmi,
- nebezpečí nárazu (naražení) pohybujícími se částmi,
- nebezpečí bodnutí nebo probodnutí nástroji nebo pinolí koníku,
- nebezpečí zlomení nástroje při práci a jeho následné vymrštění,
- nebezpečí roztržení obrobku a následné vymrštění jeho částí,
- další jiná nebezpečí (výčet není úplný).
V pracovním prostoru stroje lze identifikovat i další nebezpečí, která sice nejsou způsobována pohyblivými částmi, je však nutné je uvažovat při volbě bezpečnostních ochranných zařízení. Příčinou těchto nebezpečí jsou např. třísky (nebezpečí říznutí, píchnutí, popálení), chladicí kapalina (nebezpečí vznikající stykem se škodlivými kapalinami nebo vdechováním mlh, par a plynů, biologické a mikrobiologické nebezpečí, jestliže nastane rozklad kapaliny), emitovaný hluk (nebezpečí poškození sluchu) atd.; výčet opět není úplný. Vymezení nebezpečných prostorů a identifikování dílčích nebezpečí v těchto prostorech je nutné dokumentovat. Jeden z nejjednodušších způsobů, jak splnit tento požadavek, je znázorněn na obr. 1. 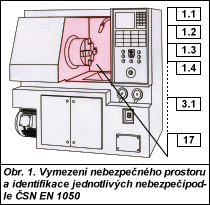 | 1.1 nebezpečí stlačení (rozdrcení) prstů, části ruky, mezi pevnou a pohyblivou částí stroje 1.2 nebezpečí střihu (ustřižení) prstů, části ruky, mezi pevnou a pohyblivou částí stroje 1.3 nebezpečí říznutí (uříznutí) prstů, části ruky, v průběhu pohybu nástroje (ale také o třísky) 1.4 nebezpečí navinutí volných částí oděvu, vlasů na rotující části stroje 3.1 nebezpečí popálení prstů, ruky, obličeje o horké nástroje, třísky nebo obrobek 17 nebezpečí způsobené vymrštěním předmětů, částí zlomených nástrojů nebo roztrženého obrobku | Pro zajištění ochrany obsluhy při činnosti stroje v automatickém pracovním cyklu (obráběcím režimu), který umožňuje, aby všechny pohyblivé části v pracovním prostoru stroje byly učiněny zcela nepřístupnými, je možné použít ochranné zařízení, přičemž z charakteru identifikovaných nebezpečí je zřejmé, že musí být použito oddělující zařízení. Nejvhodnějším řešením je použití posuvného ochranného krytu, který zcela uzavře nebezpečný prostor stroje a ve spojení s blokovacím zařízením zajistí blokování pohonů nebezpečných pohybů při otevření krytu. Kryt musí být opatřen průhledným oknem pro umožnění sledování obráběcího procesu, aby nevznikala potřeba vyřadit ochranné zařízení z funkce. (pokračování) |